Entrevistamos a… Juan José Gallego
Miembro de la línea de envasado al disolventeEntrevistamos a Juan José Gallego, Juanjo, que empezó en Isaval envasando al agua y echando una mano donde hiciera falta, hasta que el Responsable de Disolvente le dijo: “vente conmigo”, y él contestó : “¿pero solo un rato, no?” y ese “rato” se convirtió en 10 años de estrecha relación laboral.
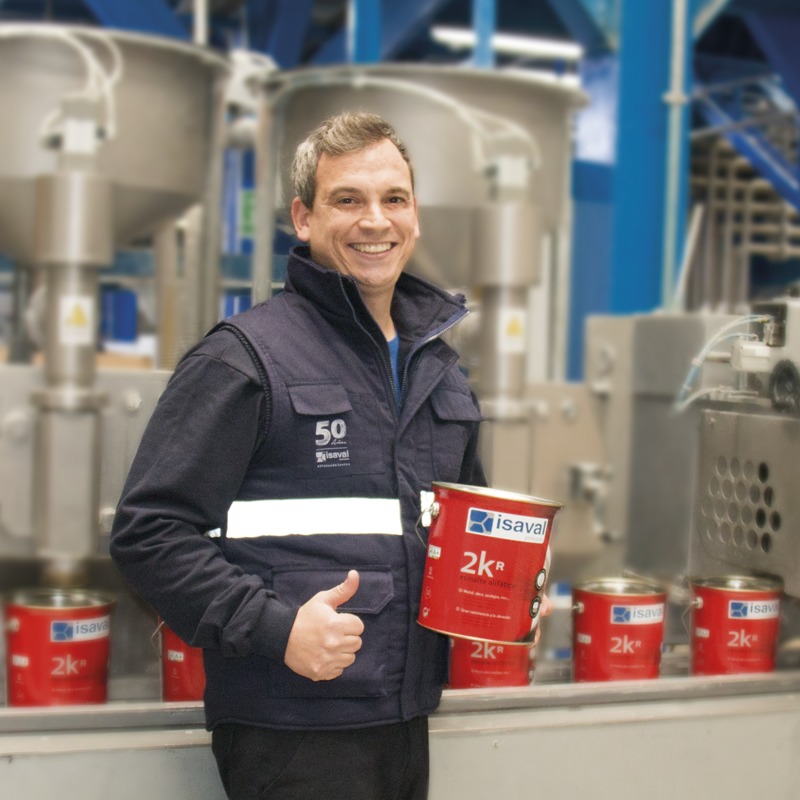
Buenas tardes Juanjo, entraste ya en la fábrica nueva, no viviste el cambio.
El cambio no, ¡pero la transición si! Cuando llegué a Isaval faltaban aún máquinas por recibir, el cableado estaba a medias, había operarios externos por todas partes… parecía Humor Amarillo. Como en casi todos los comienzos, fue duro poner en marcha el envasado, tiempos contra reloj, máquinas nuevas que no conocíamos… pero siempre sacábamos la producción adelante.
¿Cómo entraste a formar parte de Isaval?
Yo salía de trabajar en un laboratorio óptico, haciendo cristales graduados, y empecé a repartir mi CV en el polígono de Aldaia, dejando uno en Isaval. Maribel me llamó al día siguiente y me dijo “Estamos de traslado y necesitamos alguien polivalente que pueda echar una mano en lo que sea, ¿te interesa?”. Ese mismo lunes empecé y hasta hoy, más de 12 años vistiendo de azul. Podríamos decir que estuve en el momento perfecto en el lugar adecuado.
Cuéntanos el proceso de envasado, ¿cómo funciona? ¿Es igual el envasado al agua que al disolvente?
Pues empecé en envasado al agua, siendo aprendiz de Carmen con tan solo 20 añitos, toda una señora (se ríe recordando momentos entrañables y algunos difíciles de explicar). Una persona vinculada a Isaval durante toda su vida. Toda una experiencia trabajar con ella. Me enseñó todo el proceso de envasado; entonces era mucho más manual, ahora está automatizado y se lleva un control más preciso. El sistema ahora es más eficiente, desde laboratorio pasan el Parte de Envasado, con todas las especificaciones de id del producto, proporciones, endurecedor, tinte, si lo lleva, formato del envase, la producción, etc. Cuando la pintura a envasar está ya en el depósito, se conecta a la bomba correspondiente y se abren las llaves de las tolvas, que son como embudos, para cargarlas de pintura. En ese punto se calibra el primer envase ajustando el porcentaje exacto que requiere nuestro departamento técnico. Una vez obtenida la dosificación correcta, se carga la noria con los envases vacíos y el dispensador de tapas. La tolva se pone en modo automático y empieza la cadena: se llena el envase, se tapa, se cierra automáticamente, entra en el horno para flejar los botes y sale por la cinta final hasta la zona de paletizado. Al finalizar, se limpia todo a conciencia para preparar el próximo envasado. Tanto en agua como en disolvente el proceso es similar.
Aunque formas parte del equipo de envasado al disolvente, como el proceso es similar, ¿envasas algo en agua?
Si, me da igual uno que otro. Si hay que echar una mano en envasado al agua, voy encantado, allí los compañeros me tratan como uno más. ¿Aunque no esté ya la señora Carmen? Si (se ríe), el ambiente es muy bueno. Realmente estoy integrado en los dos sistemas. ¿Y los compañeros de disolvente? A veces soy algo arisco trabajando, y por eso tengo ya algunas puñaladas en al espalda (bromea). Son todos buenos compañeros. Yo me preocupo de enseñar lo que puedo a las nuevas incorporaciones, me gusta trabajar bien, ayudo a cargar el camión de residuos, tengo iniciativa, intento ir por delante, siendo consciente de que hay que hacer de todo, y echar una mano donde se necesite, “dime lo que quieres y lo hago”. ¿Y tu jefe Kiko Romero, qué tal? Confiesa… Realmente tengo dos jefes, Kiko y Lalo, me llevo bien con ellos, siempre me han tratado bien cuando lo he necesitado, pero hay que tener claro que cuando hay que trabajar y ponerse serio, me pongo serio. Ahora ayudo más a Kiko, ha delegado algunas responsabilidades en mi, desde hace poco hago funciones de organización de tareas de envasado, activar órdenes de artículos, etc. Él ya lleva muchos años y agradezco su confianza. Trabaja mucho y se lo merece. He aprendido mucho de él.
Nos comentan que no hay maquina de envasado que se te resista. ¿Cuantas controlas?
Pues sé como funcionan unas cuantas, son muchos años ya. La máquina de disolvente, la de doble dispensador de tapas y la que usamos para tintometría, la de la pintura luminiscente, el convertidor de óxido o los tintes y alguna más. Cada una tiene sus depósitos, hay de varios tamaños, dependiendo de las cantidades a producir. El más grande, tiene un sistema que nos permite un envasado más rápido. Mucho mejor.
¿Cuántos envases pueden pasar por tus manos en un día?
Depende del tipo de envase pero calculo que sobre 4.000 envases, seguro.
¿Qué nivel de seguridad hay en tu puesto de trabajo?
Es una zona de Atmósfera Átex, una atmósfera explosiva. Hay que tener la máxima higiene, están prohibidos los dispositivos electrónicos como el móvil , llevamos auriculares, botas, guantes, máscara, gafas…
Y para terminar, explícanos que es la TAPIPORLA.
(Mira al cielo y no para de reír) Cuando entra un novato, siempre hay alguien que le dice “busca a Juanma y dile que te dé la Tapiporla”, mientras va, llamas a Juanma para avisarle. Juanma le dice que no la tiene y lo manda a Jesús, Jesús a otro y a otro y a otro…, y nos vamos avisando. Al final alguien le da una pieza enorme, voluminosa y difícil de coger, que le toca hacer malabares para cruzarse la fábrica cargado y traerla. Cuando estás trabajando y ves a alguien cargado con algo así, no puedes evitar reírte.
¿Acabamos con un consejo para las nuevas incorporaciones?
Aprender de los que ya trabajamos aquí, en fábrica somos todos muy nobles y estamos dispuestos a enseñar las cosas las veces que haga falta y dar buenos consejos.